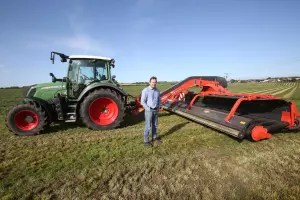
Changing the approach to grass silage making is allowing two Ayrshire dairy farms to increase milk from forage and reduce feed costs per litre.
David and Robert Veitch, brothers who both run high yielding 250-cow herds about 12 miles apart, have in the past three years switched from precision chop harvesting to using forage wagons and in the last year have replaced grass rakes with a new 9.5 metre belt merger.
Now entirely self-reliant, with no need for contractors, the brothers have total control of their grass silage making process and are producing a feedstuff that is more effective at supporting milk from forage.
“We have a forage wagon each and share the belt merger,” says David Veitch, who farms at Greenside Farm near Cumnock. “We do all the mowing, hauling and clamp filling ourselves, so have full control over when we cut and all the subsequent elements through to sheeting down.
“We’re seeing the results with the quality in the clamp and in terms of the business costings, which show that we’re making more milk from homegrown forage and cutting cost of production.”
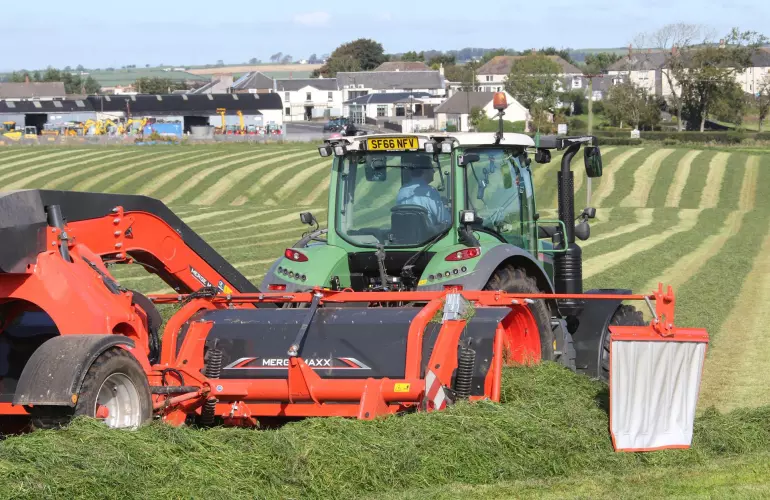
The business benefits are most clearly seen in Robert Veitch’s robotically milked herd, which averages 11,700 litres/cow. In this herd, based at Standhead Farm near Mauchline, milk from forage has in the past year increased from 1,050 litres up to 2,350 litres, with butterfat also rising from 3.6% up to 3.85%. This has resulted in a 2.2kg/cow saving in bought-in concentrates, cutting the feed cost from 12.1ppl down to 10.4ppl.
Switching to forage wagons has given greater control and produces silage with a longer chop length, and this is certainly a factor, but the replacement of twin rotor rakes with a new Kuhn Merge Maxx 950 belt merger is the more significant factor in improving silage quality.
They first saw a belt merger working on lucerne during trip to Wisconsin some years earlier, thinking then it would be a good tool for grass. Then, in 2019, they saw Kuhn exhibiting the Merge Maxx at LAMMA in 2019, eventually purchasing their machine through their local Kuhn dealer, Agricar.
“Our decision to invest in the belt merger was based on the desire to improve forage quality, which includes a reduction in soil contamination,” says David. “We have around 1,500 acres to cut across the two farms, with three or four cuts each. With the opportunity to share the machine and do some work with it for a neighbour too, this is proving a sound investment.”
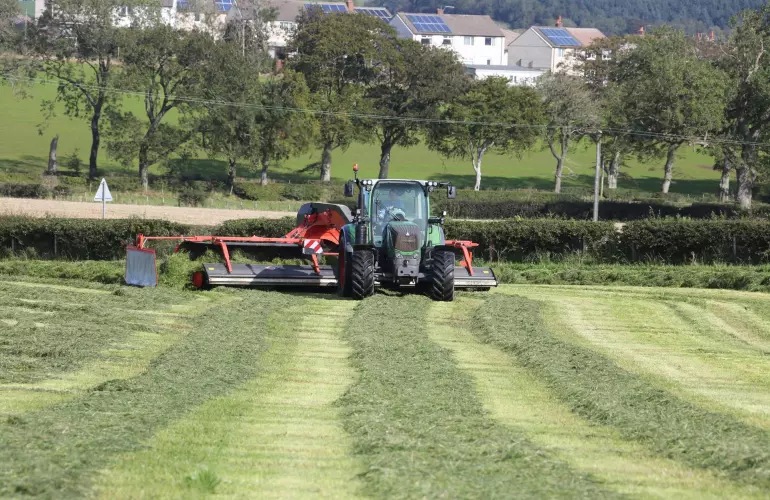
Grass is mown with a front and rear mounted mower conditioner and is left in the swath for about 24 hours before the belt merger is used to bring the swaths together. The Merge Maxx has a pick-up reel that feeds two bi-directional belts that can be operated independently, giving the machine great flexibility in how it is used. It can split the 9.5 metre pick up width two ways, bring it all into one swath, or – in the case of lighter cuts – merge 18 metres into a single swath.
“The versatility helps to give us greater operational efficiency,” adds David, “but the most notable advantage is the avoidance of contamination in the grass.
“There’s no dust being thrown up, as you see when using a rake in dry conditions, and we’ve noticed an absence of stones coming through the forage wagons. That means we’re having fewer broken blades in the machinery, which is important, but most crucially we’re harvesting grass and grass alone and not seeing soil and stone contamination in the clamp.”
The farms use a telehandler and tractor and buck rake in tandem to ensure good clamp consolidation, with the target dry matter for the silage being around 30%, which is importantly not too dry. First cut from Standhead Farm last year analysed at 11.6 ME (over 72 D-value) and 18.6% crude protein and with an ash content that showed no significant soil contamination.
Investment in technology is an important part of sustainable dairy farming for both David and Robert Veitch, and the rewards are clearly being seen on both units with their progressive approach to grass silage making.