ADVANCED BALER TECHNOLOGY DRIVES FARM EFFICIENCIES
Relying heavily on straw for its livestock system for both feeding and bedding means Grosvenor Farms in Cheshire needs to produce the perfect bale at harvest, and its latest high-density square baler has offered some considerable benefits across the farm.
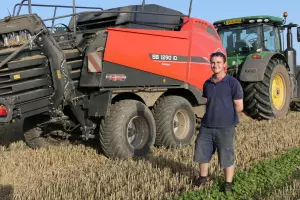
With around 900ha of cereals and oilseed rape on the estate, and a good proportion of the straw being used in the youngstock units or as an important ration component for the 2,600 milking cows, baling is a priority job where nothing is left to chance.
The decision to upgrade to a Kuhn SB 1290 iD high density square baler, using innovative twin plunger technology, was therefore not taken lightly, but according to operator Dan James, the benefits are obvious.
“Consistent size and quality of the bales is the biggest advantage,” he says, “and that’s important for everyone involved, from transport and storage through to using them. We’re not going over the top with the bale weights because they’re often being handled on units with smaller tractors, but they are well-shaped and even, so everyone knows what they are dealing with.”
Used for the first time for the 2023 harvest, the baler is an SB 1290 iD, incorporating the Twinpact double plunger system first introduced by Kuhn on its earlier LSB range. With an innovative split impact design, this allows bales with up to 25% higher density to be produced, without any increased demand for tractor power, creating the option for improved handling, transport and storage efficiencies. It’s also easier on the baler operator, reducing the rhythmical and persistent rocking that is the norm for square balers.
“We’re producing bales of around 450kg to 480kg, so well within the capacity of the baler, but optimum size for the units where they are being used,” adds Dan. “The important point is that we’re able to control the output and deliver a consistent size and an even shaped bale, whatever the conditions.”
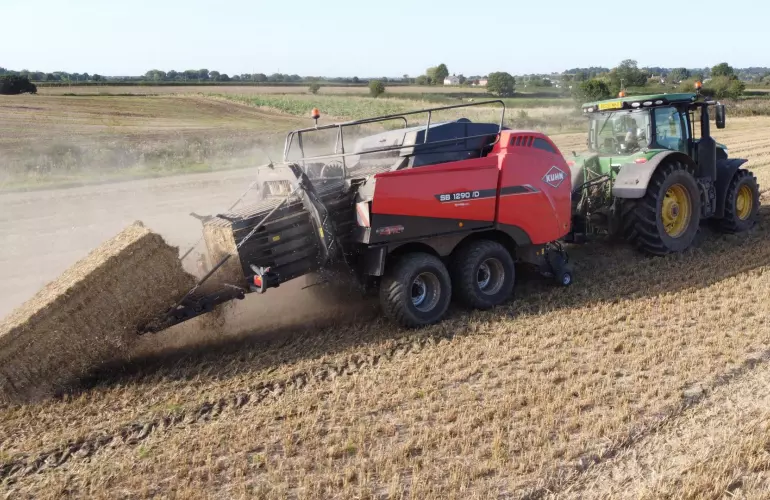
2023 was a wet summer in Cheshire, adding to the challenge for the baler operator, but the new machine coped well with the varying conditions.
“Our main combine has a 40ft cut, so it is leaving a fair-sized swath, but the crop flow into the baler has not been a problem. On the odd occasion when there’s a build up at the intake, it’s simply a case of easing off the power momentarily and the straw feeds through. In good conditions the baler has operated at up to 150 bales per hour without any problems.”
Kuhn’s SB balers have been developed with an improved crop intake system compared with earlier models. There’s a new crop guard design, and this is combined with increased torque on the rotor and feeder fork driveline, giving these models up to 15% higher intake capacity.
“We control the baler through the tractor’s ISOBUS terminal, and this gives you all the information you need to manage the crop intake and throughput,” adds Dan. “It’ll tell you if you’re getting close to the limit before there are any problems. There’s also a moisture sensor on the baler, which is a useful guide to keep an eye on conditions.”
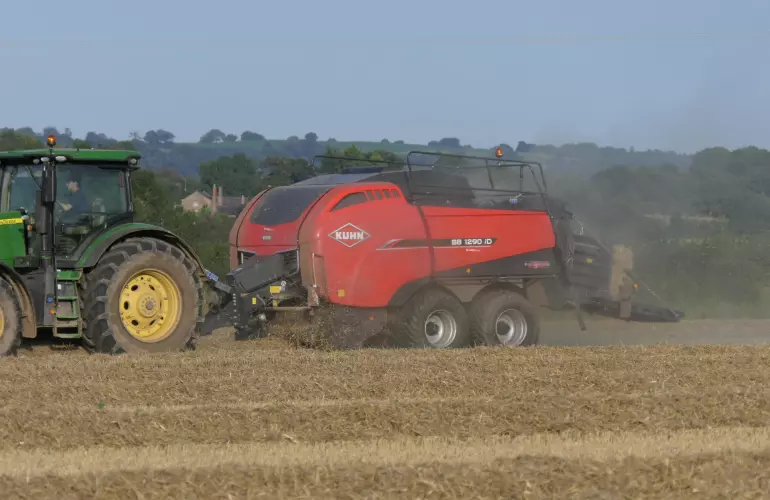
The SB 1290 iD comes as standard with a double-knotter binding system with electronic twine monitoring for increased density bales. Whilst Dan does report a small issue with one of the knotters when the baler first arrived, that was quickly sorted and there have since been no problems at all. Hydraulic fans within the knotter compartment, that continually keep the area free from debris, is another valuable feature, says Dan.
The baler is a twin axle machine and very stable in transport, with a rear steering axle when in the field for increased manoeuvrability at the headlands.
Efficiency is not only about operating capability but also routine maintenance, which is particularly important for Dan, who starts every day by cleaning and greasing his equipment.
“This baler has been designed with full accessibility for maintenance and inspection in mind, whether that’s in yard at the start of the day or anything that you might need to do in the field,” he says. “The side panels lift, allowing full access to all parts of the machine, so cleaning at the end of the day or between crops is quick and easy.
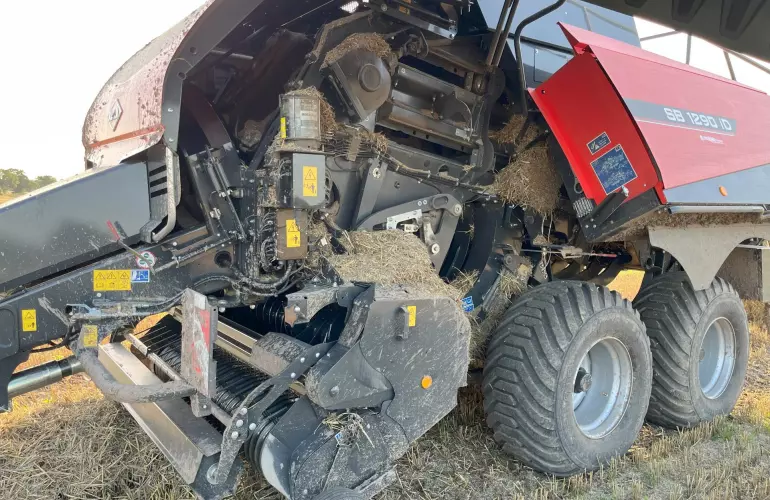
“Ultimately, it’s about the consistent size and shape of bales, which has been the stand-out difference, and also you want to have confidence in the back-up from the dealer and manufacturer,” concludes Dan.