The purpose of tedding is to spread and turn the crop sufficiently to assist drying, avoiding soil contamination in the process. Some degree of crop conditioning can also be achieved with the extent determined by the way the machine is set up. Optimum tedding performance means all the grass is handled equally and spread into an even and airy layer, avoiding lumps or wet spots, whilst ensuring as gentle an operation as possible.
The first thing is to make sure that the tedder is compatible with the working width of the mower. Ideally, this should mean that you avoid running the tractor wheels on the mown swath and that the centre of the swath is in line with the axis of the rotor. The wettest and most compact part of any swath is at its centre, nearest the ground, so it is important that the tines are set to ensure that the whole crop is lifted and that no trails are left behind.
Tine height setting
Tines should pass just above the ground at the lowest point when the machine is in work, and the best way of getting this right is to set the tines at stubble height when stationary. If the field is uneven and there is a concern over soil contamination, set tine height marginally higher. Height adjustment will be achieved on most machines through a combination of wheel and top-link settings.
Top-link setting will also determine the angle of the rotor. This, together with the speed of rotation relative to tractor forward speed, is crucial to tedding performance.
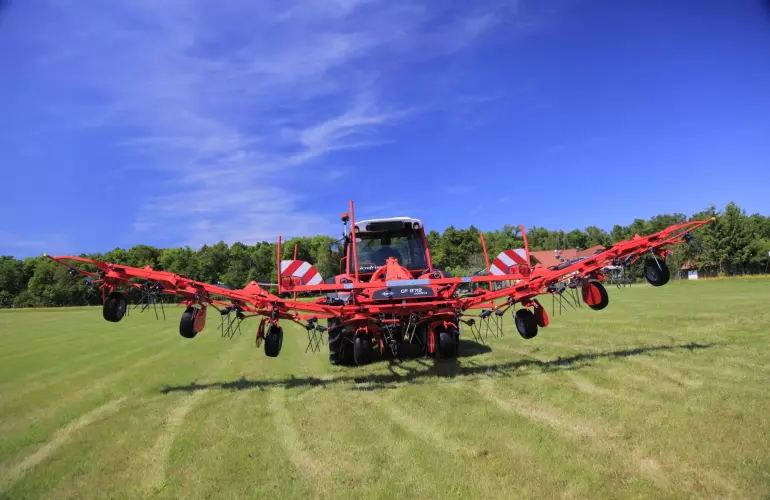
Rotor angle
Rotor pitch angle and rotor speed should be set in order to lift the crop into the air and turn it once. If the angle is too low, lumps will form, and if speed is too great, the crop will be flattened due to excessive projection speed. Set up should be done in an area of the field most representative of the average crop density, assuming that it is reasonably even across the field. Where density varies, for example on the headlands, adjustment should be made to tractor forward speed and rotor speed. As a rule, a higher crop density needs a higher rotor speed and slower forward speed.
Ease of adjustment
Points to bear in mind when comparing machines relate to rotor configuration, rotor drive system, ease of adjustment, tine safety and transport width.
In general terms, smaller rotors with greater numbers of tines will perform better, and drive systems are relevant from the point of view of ensuring consistent rotor speed across the full working width. Ideally, adjustments should be possible without the need for tools, and tine safety straps are recommended if you want to avoid the risk of metal going through the forage harvester. When it comes to transport, height - as well as width - should be a consideration.
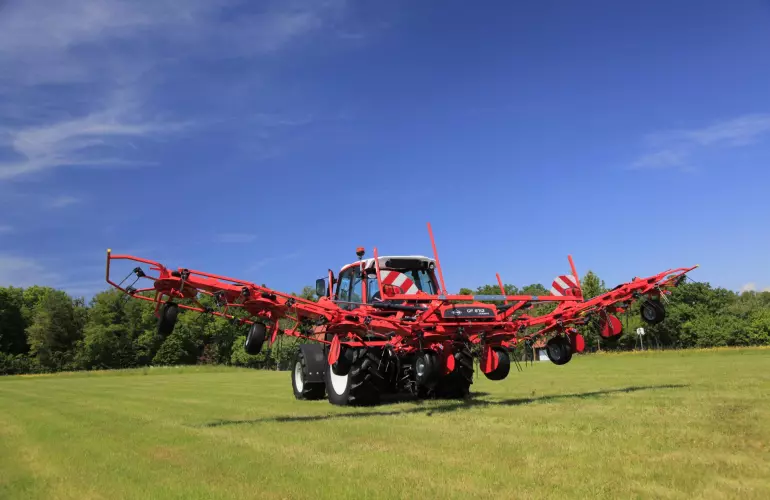
CASE STUDY: Versatility suits contractor’s needs
Gloucestershire farmer and contractor Nick Keyser is a grassland specialist, making close to 10,000 large square and round bales a season as silage, haylage or hay.
Operating within a 30 mile radius of Cirencester, he’s dealing with a variety of situations for a range of customers, but all require a quality forage product made to a specification.
His tedder is integral to his grassland operations and before his recent upgrade he did a thorough review of the market, testing several machines before opting for his Kuhn GF 10812 Gyrotedder. A mounted machine with a working width of close to 11 metres, it’s one of the larger machines in the latest generation of tedders from Kuhn.
With the capacity for medium to large-scale operations, this Gyrotedder is also suited to working in tight, awkwardly shaped fields, so ideal for someone like Nick, who runs his on a 165hp tractor.
“I wanted a mounted machine with a good working width,” he says, “and this machine offers that as well as being relatively light and compact for transport.”
It’s compact transport position, made possible by a patented stabilisation system between the headstock and the frame, also enhances the machine’s stability during work. This is a factor in its field performance, alongside features like the hydraulic top link, adjustable rotor speed and Kuhn’s unique Headland Lift Control feature.
“We tend to tweak the top link as we go and vary rotor speeds quite a lot in order to achieve the best results that we can,” adds Nick. “Headland Lift Control is another stand-out feature that contributes significantly to the machine’s overall performance.”
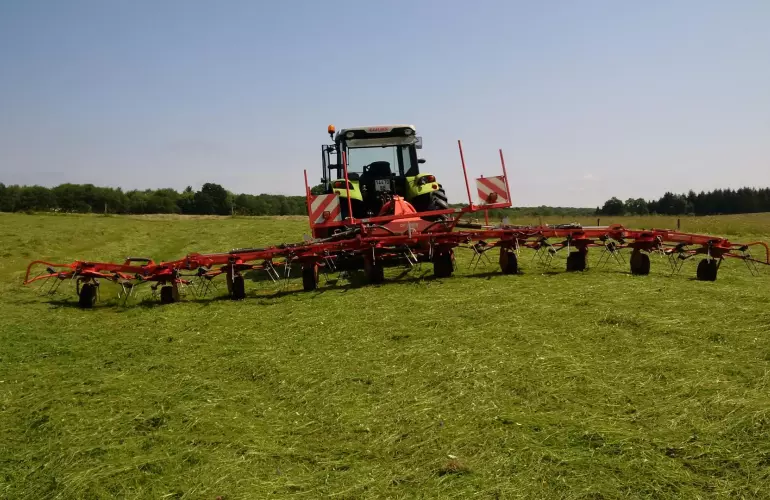
Headland Lift Control, standard on the GF 10812, lifts all rotors to a height of 50cm in less than 5 seconds, making it easier to manoeuvre and operate the tedder, especially on tight headland turns. The fast-acting rotor-lift system also helps to reduce the risk of impurities being introduced into the forage.
As with all Kuhn Gyrotedders, the GF 10812 is equipped with the Digidrive multiple finger coupling rotor drive system that allows transmission of power at constant speed at angles of up to 180 degrees. In addition, pivoting small diameter rotors and asymmetrical tines improve ground contact and reduce soil contamination, while wheels which are placed close to the tines improve ground following. Hydraulic adjustment for border tedding is also available as an option.